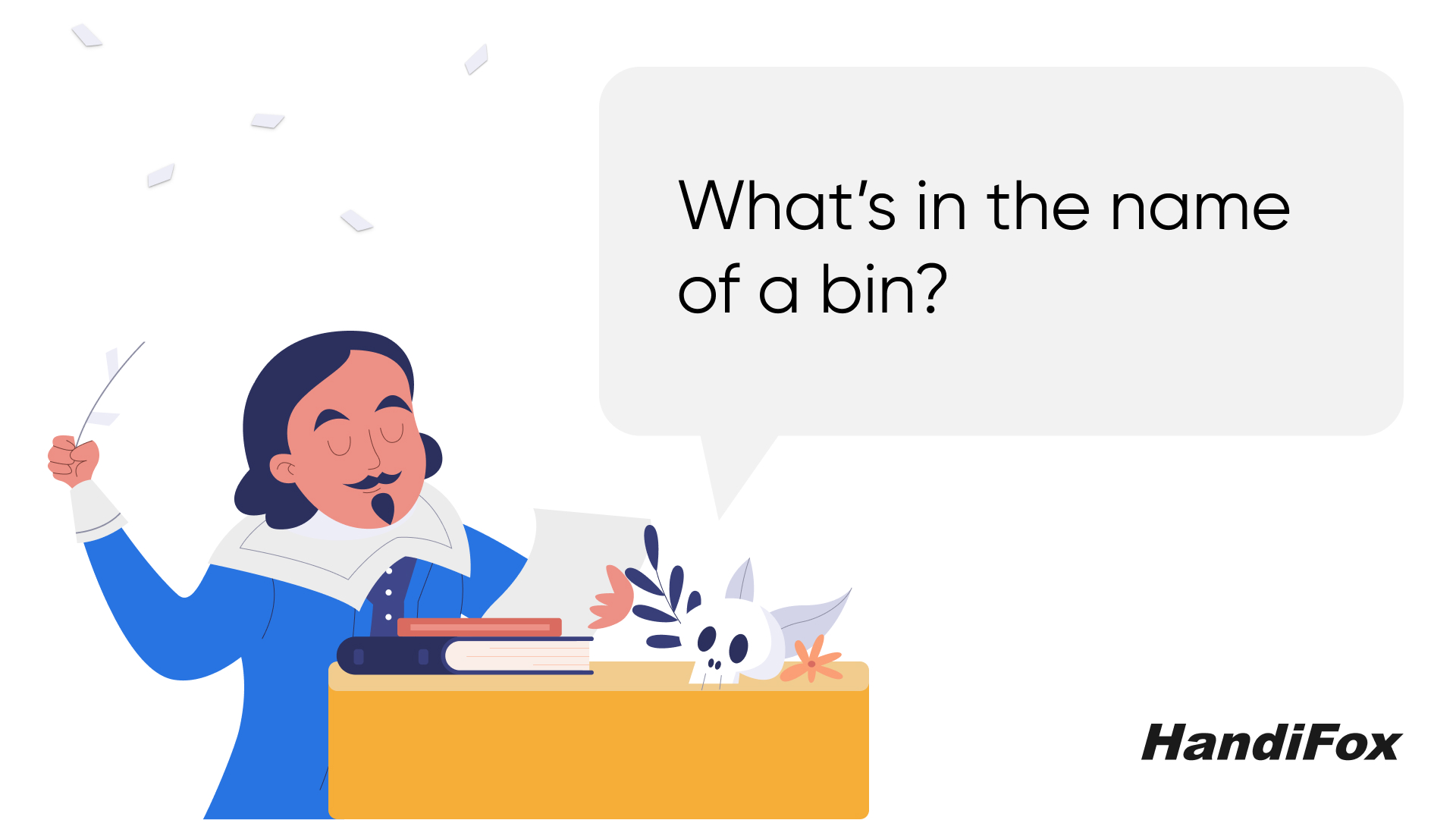
Bin location tracking is one of the most trivial yet overlooked inventory management practices that dramatically impacts your ability to handle inventory effectively. This blog post will explore how proper bin location naming can streamline operations and how bin tracking boosts overall productivity for business owners.
Naming and tracking bins. Why bother?
Bin tracking is very much like knowing an apartment number when you are visiting a friend who lives in a many-storeyed building. Without this navigation, your stockers and pickers do a lot of unnecessary legwork while looking for, moving, counting, and putting inventory away. The ability to read the item’s address in a matter of seconds, and spend the minimal travel time getting there is what bin location tracking for. This brings us to another crucial aspect - bin location naming.
Proper bin naming is paramount to boosting the efficiency of your bin location system. Here is why:
Enhanced Inventory Accuracy
When bin locations are logically named and easy to understand, it reduces the chances of human error. Employees are less likely to misplace items, leading to enhanced inventory accuracy.
Streamlined Picking and Packing
A uniform bin naming policy ensures that employees can find items quickly and efficiently. This streamlined process not only accelerates picking and packing operations but also minimizes errors in order fulfillment.
Improved Warehouse Layout
Proper bin location naming allows for an organized and systematic warehouse layout. It makes it easier to designate specific areas for different types of inventory, improving overall workflow.
Designing a consistent warehouse bin location matrix
Every warehouse is built and organized with the business’ qualities in mind but, generally, there is an aisle-section-shelf-bin matrix. So, bin is the smallest storage sub-location there is in a warehouse.
Breaking Down Your Space
Divide your warehouse into manageable subspaces. This is particularly useful if you have a large storage area. Name each zone using alphabetic characters or numbers to create the first element of the bin location code. For example, if you’re looking for a unit in zone Z1, the initial part of the location address would be Z1-..-..-..-.. .
Once you reach the aisle level, further divide it into sections, shelves, and bins. Each section should be clearly numbered from bottom to top and left to right. For instance, if you’re in aisle A1, section S2, shelf SH3, and position P1, the complete bin location code would be Z1-A1-S2-SH3-P1.
3 big don'ts of setting up bin location systems
1. Don't overcomplicate the system
Ensure the system provides enough detail to be useful without becoming a burden for staff to use and maintain.
2. Don't neglect employee training
Failing to adequately train employees on the new system can lead to errors and inefficiencies. Provide ongoing support and refresher training to accommodate new employees and address any issues that arise.
3. Don't forget to integrate with inventory management software
Ensure the bin location system is fully integrated with your inventory management software. Make sure that any changes in bin locations or inventory are updated in real time in the inventory management system to maintain accuracy.
Bin tracking as part of your inventory management system
Inventory intake, putaway and pick/packing are the most resource-intensive tasks within a warehouse. You can have automated inventory system with barcoding and everything, but if you don’t have Bins as a feature, much of this optimization falls flat. This lack of guidance for warehouse workers is the #1 time killer that converts into excessive labor costs.
Bin tracking is normally part of advanced warehousing and is not available in QuickBooks Desktop until the Enterprise version. QuickBooks Online doesn’t have it. Meanwhile, both HandiFox Desktop and Online both offer bin location as a text field that you can fill out with bin adresses of any format based on your warehouse layout. Bin location tracking is a setting that you can enable or disable at any time.
As HandiFox Desktop follows QuickBooks Enterprise, it can pull bin addresses for every single product on the item list from QuickBooks and push them into the HandiFox mobile app. So, your stockers/pickers are able to use their phones to
- assign/reassign bins to items when generating a PO
- see products’ bin IDs while receiving stock against a PO
- use bin locations on pick lists to increase the picking speed and reduce picking errors
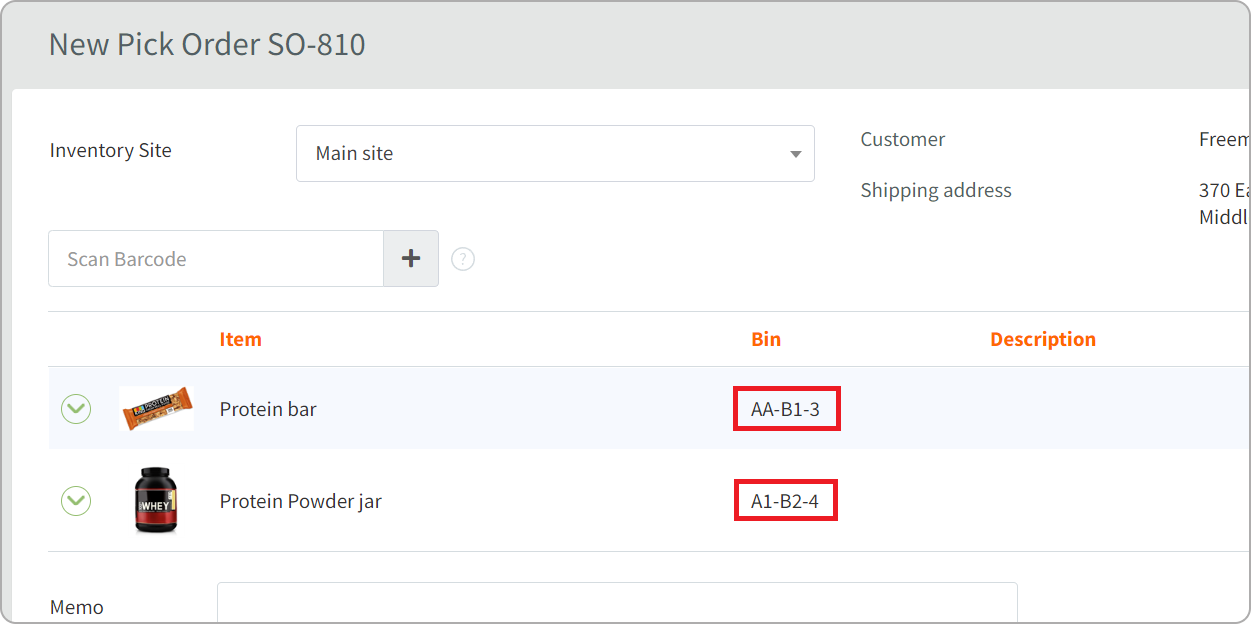
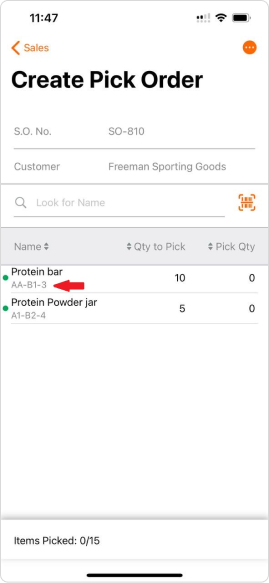
In HandiFox Online, whether it’s counting, transfer, receipt or pick&pack, bin addresses will be in all of your transactions, both in the web and mobile apps.
Practical Tips for Setting Up Bin Locations
Start Small and Scale Up
Begin by organizing a small section of your warehouse. Once you’ve nailed down the naming system and ironed out any kinks, scale up to the rest of the warehouse. This phased approach allows for adjustments without disrupting entire operations.
Involve Your Team
Get input from your warehouse team when designing the bin location matrix. They are the ones who will be using the system daily and can provide valuable insights into what will work best. Collaborative efforts lead to a more efficient and user-friendly system.
Regular Audits
Conduct regular audits to ensure that the bin location system is being followed correctly. These audits help identify any discrepancies or areas that need improvement, keeping the system running smoothly.
Consistency is Key
Use a consistent method for naming bin locations to avoid confusion. A standardized approach ensures that all employees are on the same page, reducing the likelihood of errors. Consistency also makes it easier to train new staff, as they can quickly grasp the naming system.
Visible Labels
Ensure that all sections, aisles, and bins are clearly labeled and easily visible. This visibility helps employees locate items quickly, improving overall efficiency. Consider using large, color-coded labels or signs to make navigation even easier.
Adapting to Your Warehouse Layout
While the 'Aisle, Section, Shelf, Bin' configuration is standard, adapt the naming system to fit your warehouse’s unique layout. Flexibility in your approach allows you to optimize the system for maximum efficiency.
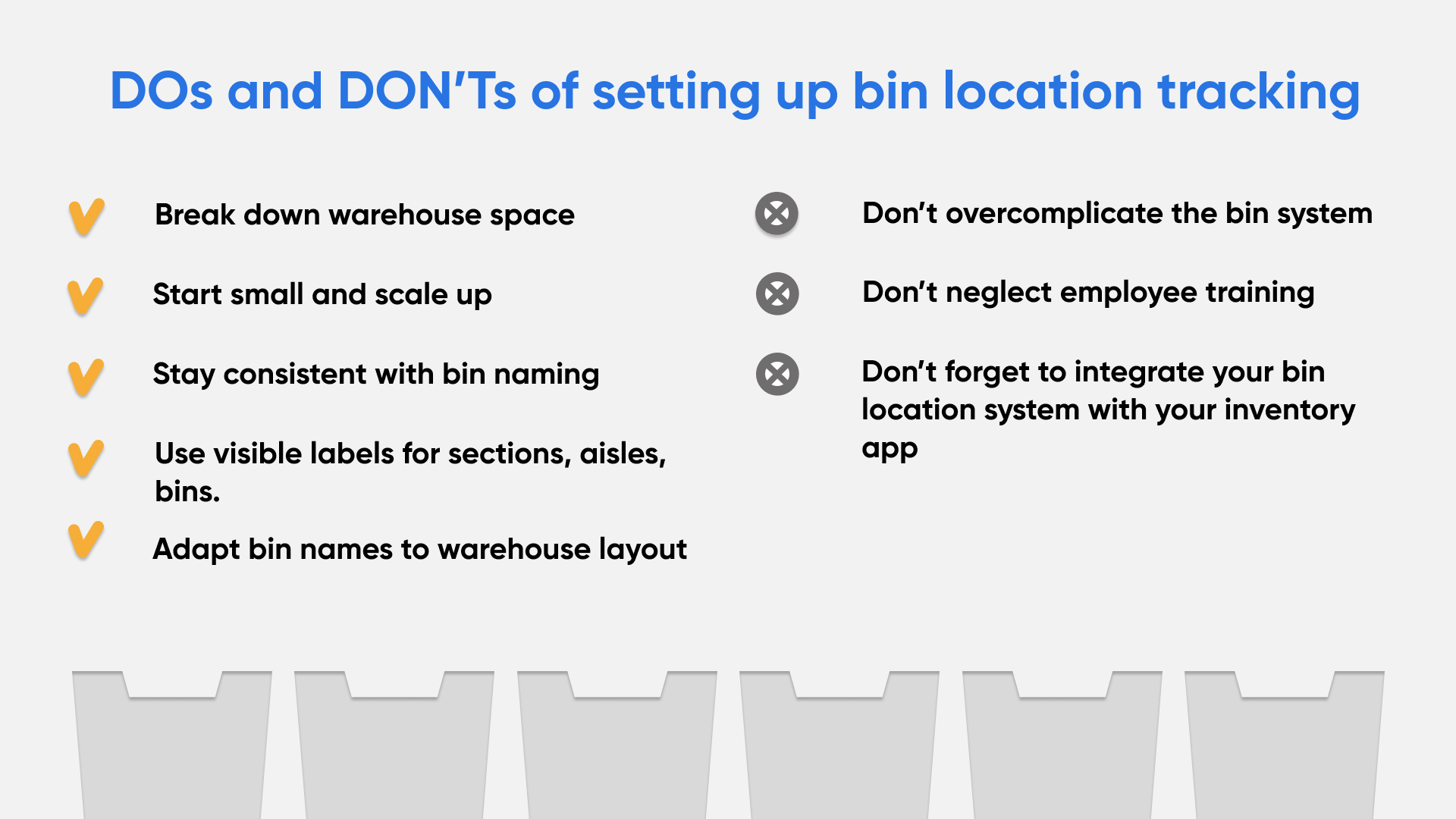
Saved time is what small inventory-centered businesses value over anything else. Bin location functionality is one of the time savers most SMB owners hope to get when purchasing inventory management software. Even if your inventory control system doesn’t support bins, you can do without them and be fine. But why settle for ‘fine’ when you could do great? Get the most out of automated inventory management software - try HandiFox.