Barcodes have seamlessly blended into our lives. What can be barcoded gets barcoded to give us the speed today’s fast-paced world requires. This guide explains the nuts and bolts of barcoding and helps small businesses get barcoded with minimum time investment.
Why do small businesses need barcoding?
The simple answer would be that they aspire to become bigger one day. No growth is possible without streamlined operations. These are some benefits barcoding was developed to provide as a technology.
- A time- and work-saving tool. A barcode inventory system at hand increases your warehouse and order processing productivity. Identification and validation via a quick barcode scan takes way less time than when warehouse personnel go around the storage area and ‘read’ product names while hunting down items on their pick lists. This inefficiency cuts into labor costs.
- Maximizing accuracy. Barcodes significantly reduce the chance of human error in inventory tracking. By making it ubiquitous throughout the entire supply chain, from receiving inventory to selling at the customer’s door, you’re significantly improving your small inventory-centric business's front and back ends.
- Compliance and standardization. Many industries have standards that require the use of barcodes for tracking and identification, ensuring compliance with these standards. It facilitates international trade by complying with global standards such as GS1 (we’ll cover this type of barcode a little further).
- Scalability. As your business grows, barcodes can easily scale with you, accommodating an increasing number of products and transactions without a significant increase in overhead.
The anatomy of barcodes. What types are there?
Generally, there are two types of barcodes - 1-dimensional and 2-dimensional.
The linear or 1D barcodes feature a group of barcode types that vary in the use of different symbology. UPC (North America), EAN (Europe), Code39, and Code128, are the most widely recognized 1D barcodes. The main difference between the types lies in the length and density, as well as the geography of usage (UPC vs. EAN). Both Code39 and Code128 are alpha-numeric but the latter is of a higher density.
A good example of a 2-dimensional barcode would be a QR code. This type is getting more and more widely used, if not to say preferred over 1D barcodes. QR codes can hold significantly more data but aren’t necessarily the best choice - consider your business’s priorities and needs.
If you want your products to be sold in other stores, you will have to license a company prefix with the GS1 organization and purchase GS1-certified barcodes for your inventoried items.
Why do GS1 barcodes stand out?
GS1 is a not-for-profit organization that develops standards for, controls, and manages the use of particular types of barcodes, both 1D and 2D (see the list here). GS1 DataBar barcodes are advanced 1D barcodes with embedded data. Unlike other 1D barcodes that have only so much as a product’s name encoded within, GS1 DataBar barcodes hold a lot more information about an item. These data-embedded barcodes can tell you what the product’s lot number, serial number, expiry date, quantity, weight, and company code are. Scanning GS1 DataBar reduces checkout time - only one scan lets the computer know so much about the product leaving the store.
What are the main parts of a barcode system?
A barcode system consists of several key components that work together to encode, capture, and process data. Here are the main parts:
- 1D or 2D barcodes
- Barcode scanner
- Barcode printer/ Label printer
- Software integration (accounting, inventory, or POS)
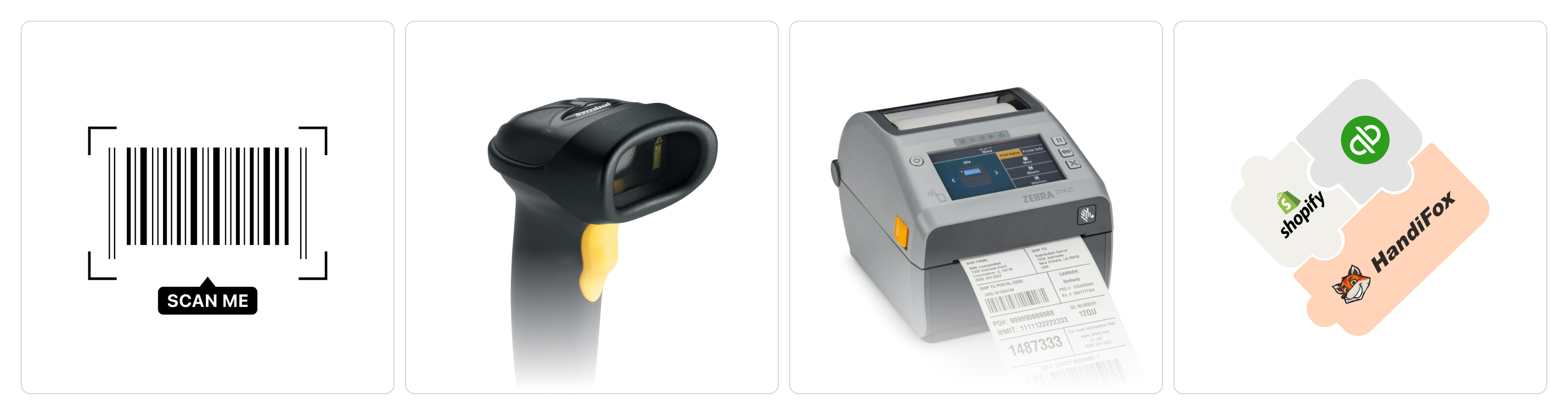
Each of these components plays a crucial role in ensuring the efficient operation of a barcode system but some parts aren’t mandatory depending on your business needs. An inventory management solution normally incorporates all the mentioned parts and eliminates the need for too many additional barcoding bells and whistles
How to set up a barcode system?
Whether you’re intending to use the existing barcodes of the products supplied to you or generate new ones for internal use, you’ll need to:
- Create a database of barcodes
- Assign them to products
- Print labels
First, you’ll have to get a barcode scanning tool and software that works with it. What we encourage HandiFox users to do in the first place is check the compatibility of their hardware with their software. Generally, there are three barcode scanning options:
.jpeg)
More on how to choose one from a humongous assortment and what the best barcode scanning tools for small businesses are is in our free guide.
Once you’ve purchased a scanner, you need to get your inventory barcoded. All the leading inventory management apps are up to the job, HandiFox included.
HandiFox can record existing barcodes or generate new ones. This could be done in a batch or one by one, depending on the number of SKUs your business stores. Once your inventory is barcoded, you can scan products during lookup, counting, stock intake, picking/packing, and selling. Generally, the workflow is as follows:
Barcode Generation and Printing:
- Generate barcodes for new products within the software.
- Print barcode labels and affix them to products, shelves, or storage bins.
Receiving Inventory:
- Scan incoming products using barcode scanners.
- The software updates inventory levels in real time and stores details of received items.
Inventory Tracking:
- Scan barcodes during inventory counts to ensure accurate stock levels.
- Track product movements within the warehouse or between locations by scanning barcodes at each point of transfer.
Order Fulfillment:
- Scan barcodes during order picking to ensure the correct items are selected.
- Update inventory levels automatically as items are picked, packed, and shipped.
Sales Transactions:
- Scan barcodes at the point of sale to quickly add items to the sales transaction.
- Inventory levels are updated in real time as sales are processed.
The HandiFox inventory software can print 1D and 2D barcodes, letting you customize what goes on the label (price, serial/lot/expiration date, description, etc.).
Barcode printers or standard office printers?
Choose barcode printers if:
- You have high-volume barcode printing needs.
- You require durable, high-quality barcodes that can withstand various environmental conditions.
- You need to print on a variety of label materials.
- You seek integration with inventory management or other barcode-related software.
- You prioritize efficiency and speed in printing.
Choose standard office printers if:
- Your barcode printing needs are low-volume or occasional.
- You are operating on a tight budget and need a cost-effective solution.
- You require a versatile printer for multiple office tasks.
- Durability and precision are less critical for your barcode labels.
It wouldn’t be an exaggeration to say that barcoding is one of the deciding factors in the success of your small business. Barcoding software like HandiFox can take upon itself most of the related tasks like generating, printing, and reading barcodes. Once you’ve introduced barcoding into your workflows, the saved time can be reallocated to higher-level tasks. Get barcoded one step at a time with this ultimate guide.