Making a mistake while stock-taking, counting, or order packing may seem like no big deal to a warehouse worker. But any small business owner knows that in today’s highly competitive business environment, the stakes are high. As a result, managers put extra pressure on warehouse personnel to try and avoid making inventory mistakes altogether. Instead, they could overcome FOMU (Fear of Messing Up) by recognizing errors and making their inventory management more resistant and flexible to swiftly fix those blunders.
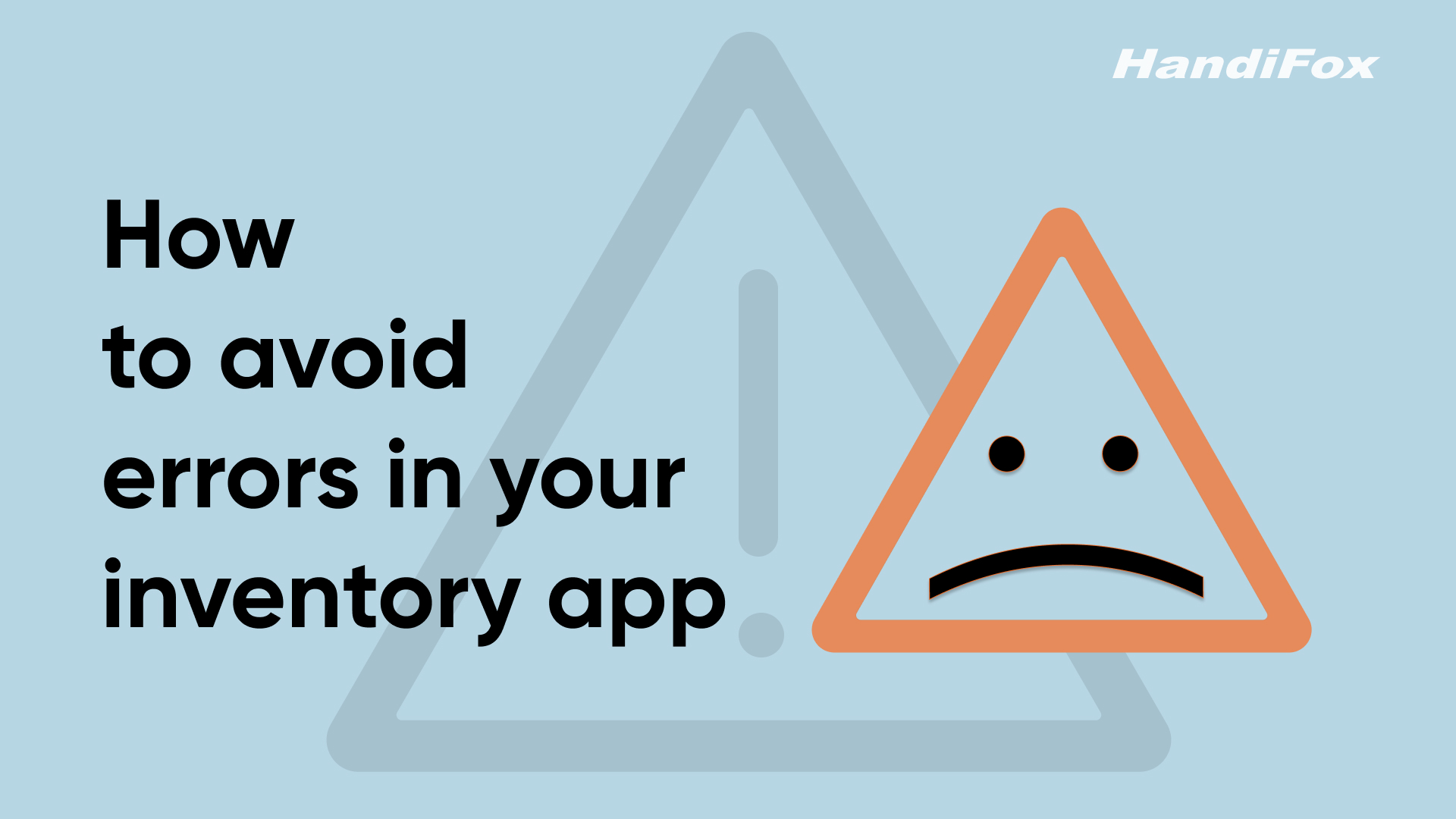
The most common errors that happen while using inventory management apps
1. Data Entry Errors
- IncorrectiItem scanning: mis-scanning items or entering incorrect item codes can lead to discrepancies.
- Human input mistakes: even with automation, manual data entry is sometimes required. Errors can occur if the wrong quantities, prices, or descriptions are entered.
2. Integration Issues
- Incompatible systems: Failure to properly integrate the inventory software with other systems like accounting can result in data mismatches and operational inefficiencies.
- Sync failures: delays or failures in synchronizing data between different systems can cause outdated or incorrect inventory records.
3. Inaccurate stock levels
- Incorrect initial setup: errors during the initial setup phase, such as incorrect starting inventory counts, can cause ongoing inaccuracies.
- Unaccounted stock movements: stock movements (such as returns, damages, or misplacements) that are not recorded in the system can lead to inaccurate stock levels.
4. Software configuration mistakes
- Incorrect settings: improper configuration of software settings (e.g., reorder points, unit measurements) can lead to errors in inventory management.
- Outdated software: using outdated software versions without applying necessary updates can lead to bugs, vulnerabilities, and compatibility issues.
5. Human oversight
- Neglecting system alerts: ignoring or overlooking alerts and notifications generated by the software (e.g., low stock alerts, reorder alerts) can result in stockouts or overstocking.
6. Barcode errors
- Barcode misreads: Damaged or incorrectly placed barcode tags can lead to scanning errors and incorrect data entry.
7. Poor data management
- Duplicate records: Having duplicate item records can cause confusion and inaccuracies in inventory counts.
- Data corruption: corrupted data due to software glitches, power outages, or hardware failures can lead to loss or misrepresentation of inventory information.
8. Inadequate Reporting and Analysis
- Ignoring reports: failing to regularly review and analyze inventory reports can result in missed insights and unresolved discrepancies.
- misinterpretation of data: misinterpreting inventory data and trends can lead to poor decision-making and inventory management practices.
9. System Over-Reliance
- Over-reliance on automation: relying too heavily on automated systems without periodic manual verification can result in undetected errors accumulating over time.
10. Technical Issues
- Software glitches: bugs or technical issues within the software can cause incorrect data processing or reporting.
- Hardware failures: problems with hardware components (e.g., scanners, servers) can disrupt the inventory management process.
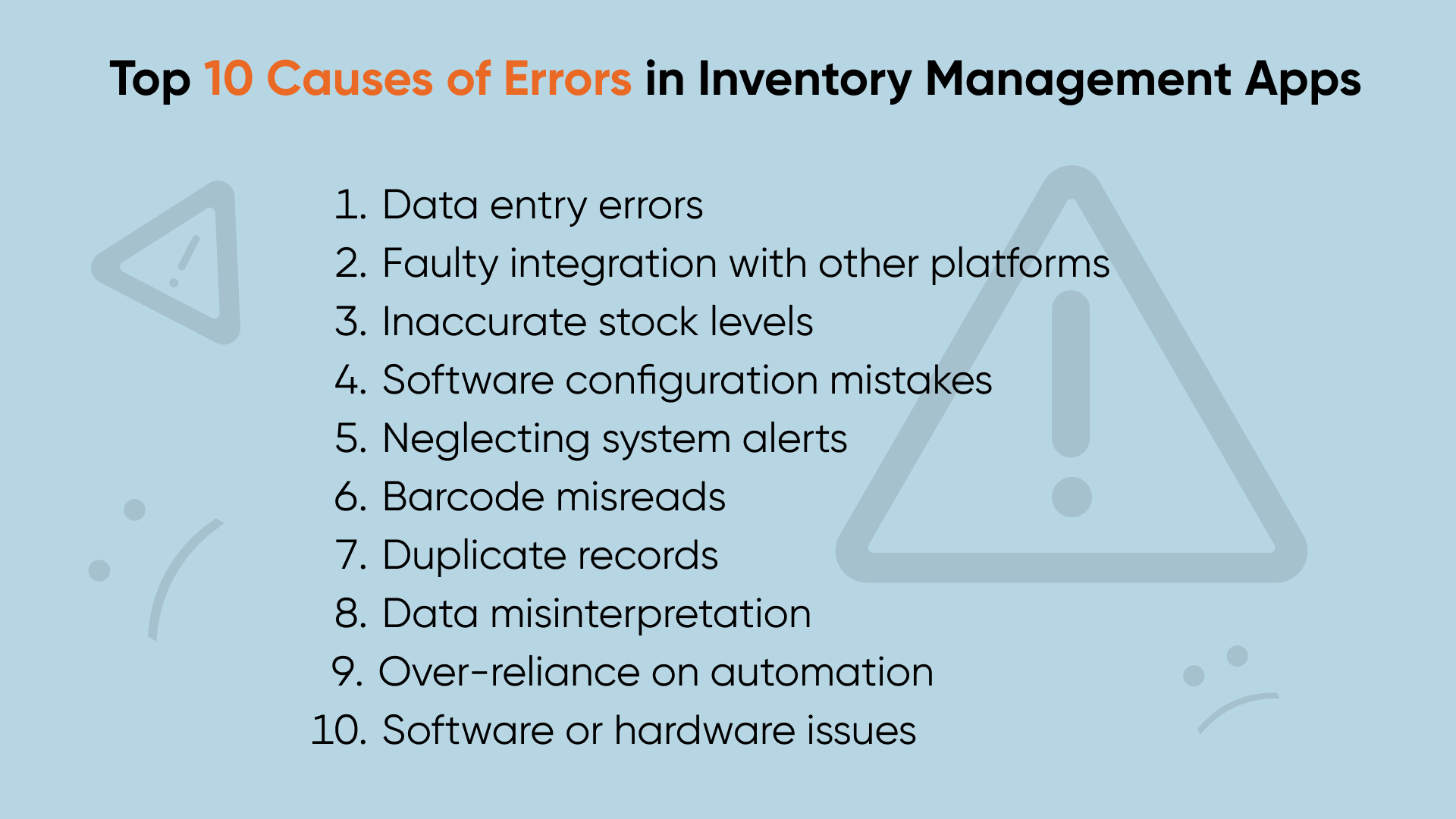
The Fear of Messing Up (FOMU) can be overcome in 3 steps
Messing things up at one step could have a domino effect and cause you to have trouble making inventory records add up, getting to the bottom of problems, or, ultimately, losing clients to your errors. Meanwhile, making mistakes is human nature. Luckily, there is a lot you can do to get a better handle on that.
- Deactivate legacy items in QuickBooks. A lot of errors-to-be are nesting in your QuickBooks inventory list right now. There might be duplicates, products that you’ve stopped selling long ago, or those that your supplier has discontinued. You know better than to just let all of this be, right? You might want to review the list of products and services first to ensure it’s up-to-date. To be honest, it’s not exactly a quick and enjoyable process as you’ll have to go and review them one by one in QuickBooks (applies to both Desktop and Online) manually. To go faster, you can use the filtering, set up a date range, or go category by category. Good tip! Deleting these items can mess up your books as they used to be associated with transactions. You might want to simply make them inactive to avoid any inconsistencies in the future.
- Finding a 3rd party inventory control app that can sync back to QuickBooks. Managing inventory in QuickBooks isn’t as quick, intuitive, accurate, and informative as you’d want it to be. Third-party inventory apps, on the other hand, let you bring order, automation, efficiency, and data-driven decision-making into daily operations without losing the link to QuickBooks. Above all, they are meant to reduce error at all steps. QuickBooks has a 3rd-party app store with real-user reviews to help you look for the one that suits you best.
- Enable barcoding throughout inventory, purchasing, and sales processes. Despite the era of high-tech, a lot of small businesses seem to be struggling to get into the 21st century. The speed and accuracy of barcoding technologies are something they are still missing out on.Barcoding is available in QuickBooks Desktop with Advanced Inventory but QuickBooks Online doesn’t have it. That’s where QuickBooks third-party inventory apps step in to fill the gap. To exemplify, HandiFox allows reading, recording, and generating barcodes. It also helps create barcode labels to put on products for a more efficient search and quicker entry on transactions.
7 things that make inventory management error-resistant in HandiFox
Here is a list of preventive mechanisms we’ve built into HandiFox to bust errors:
- Barcoded inventory
- Automatic syncing with QuickBooks
- Not being able to create transactions with items that aren’t available
- Transactions with insufficient item quantity or wrong lot numbers get blocked
- Ability to review inventory counts before applying them
- Checking incoming stock against POs
- Pick/pack verification of outgoing stock
On top of that, if mistakes do slip in, they can be easily traced back to the transactions and users who made them.
Mistakes, however small, can spiral into bigger problems making you spend hours reconciling inventory records to right the wrong. By being aware of these common errors and taking proactive measures to prevent them, businesses can optimize the use of automated inventory control software and maintain accurate inventory records. Enjoy error-resistant inventory control with HandiFox - take a free trial now.