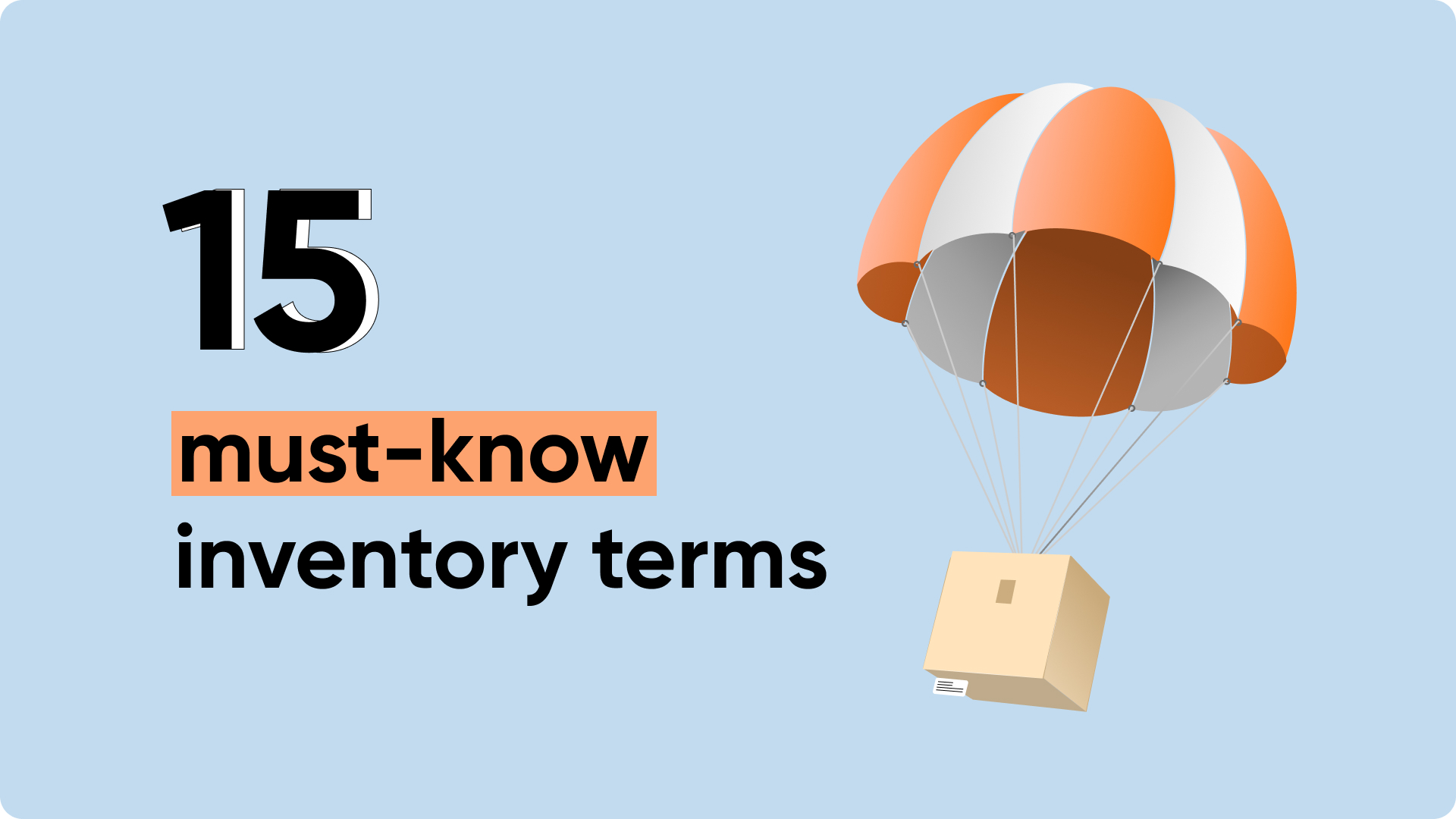
Technology has been accumulating the professional wisdom and experience of warehouse managers for decades now. The inventory software of 2025 is nothing less than the playbook of efficient inventory control. To use these tools effectively, you must understand the inventory terms they have adopted.
Though terminology may differ from app to app, there are at least 15 basic must-know terms.
1. Inventory
Inventory is a company's tangible assets in the form of finished goods or raw materials meant for sale, resale, or production. Such items have to be tracked and accounted for through consistent record-keeping. Generally, four types of inventory are recognized:
- Raw materials
- Work-in-progress goods
- Finished goods
- Maintenance, repair, and operations inventory (MRO)
Raw materials are the materials used during production or manufacturing.
Work-in-progress goods are partially finished goods that are still in production.
Finished goods are the end-products of the manufacturing process or simply items you purchase from vendors to sell to your customers.
MROs (maintenance, repair, and operations inventory) are the items that support your operations, like supplies, spare parts, etc. In some inventory systems, they’re alternatively called non-inventory items. Some stock control systems log their quantities, while others don’t.
If your company is a field service business, you must keep track of your intangible products - your services. To this end, inventory tracking software like HandiFox Online introduces service items. You can add services alongside tangible products to your transactions.
2. Stock Keeping Unit (SKU)
An SKU, or stock keeping unit, is a unique identifier assigned to a product that helps in organizing and cataloging items. SKUs are used to distinguish between different products, variants, or versions. They are alphanumeric or numeric.
Here’s a screenshot with an item list from HandiFox Online, featuring all the key data, including the SKU, related to products in a company’s inventory.
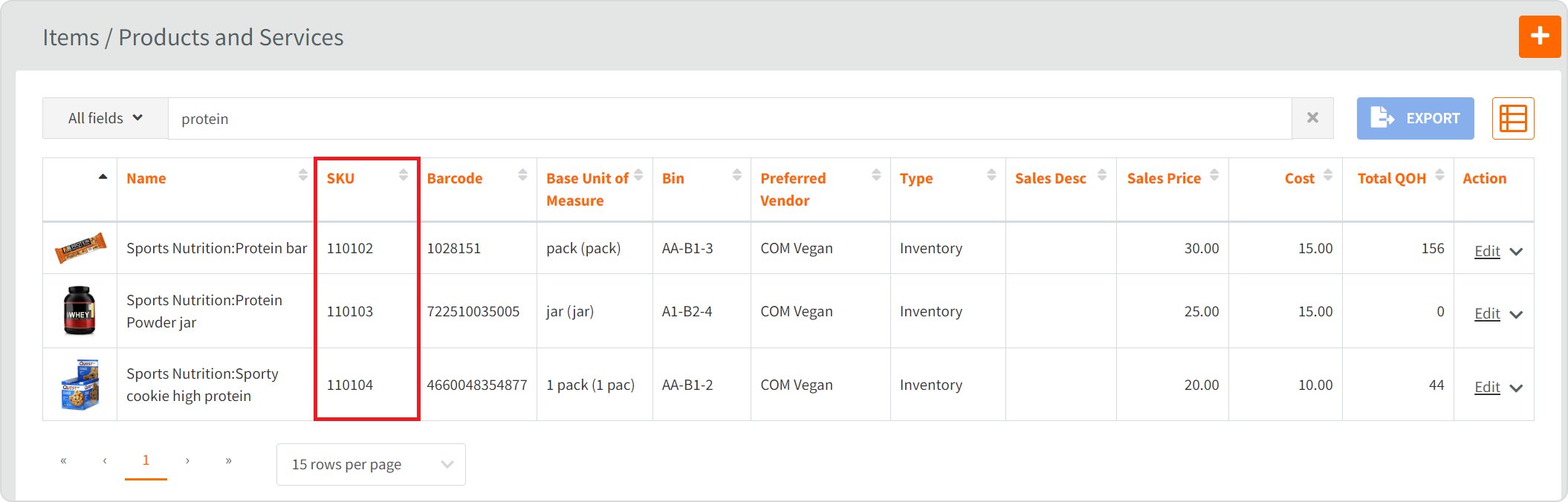
3. Reorder Point
A reorder point is the minimum quantity you would like to have in stock at all times.
Stock management systems track items whose quantity is below their reorder points and suggest including them on the next purchase order for restocking.
Some apps can even do it automatically - all items currently below their reorder points get added to a replenishment order, with a quantity that will bring it up to its desired quantity on hand (the detailed explanation of the term coming in a bit).
HandiFox allows setting up reorder points for individual or all items in one go across several warehouses.
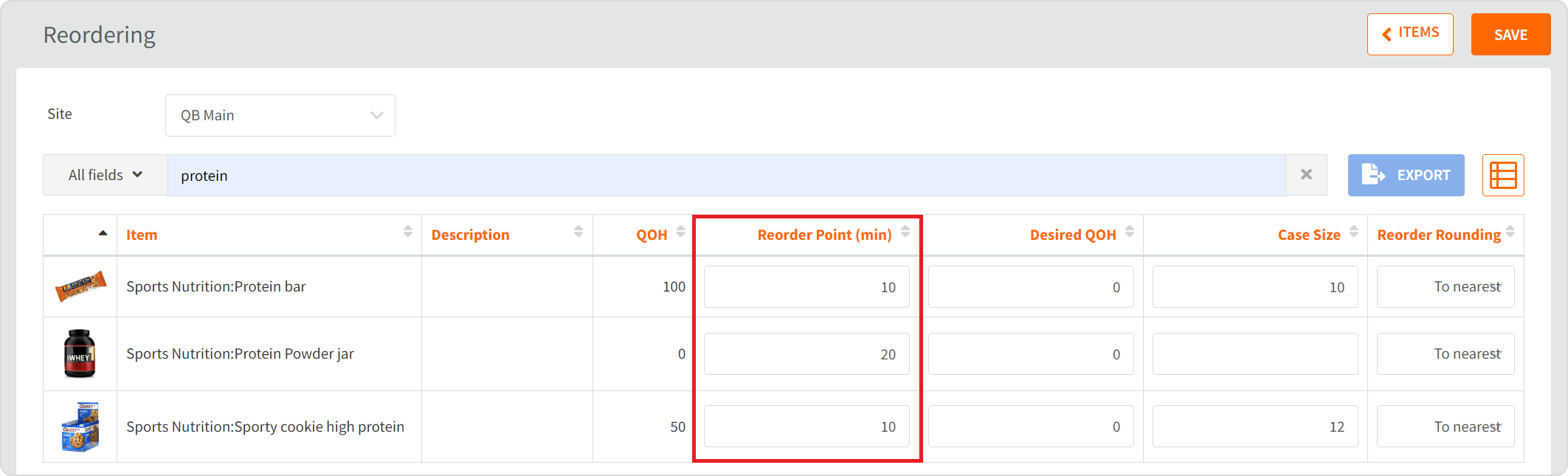
4. Desired Quantity on Hand
A desired quantity on hand is the target level of inventory that you prefer to have on hand at all times.
Not all stock tracking systems have this feature - most of them offer reorder points only. HandiFox uses both reorder points and desired quantity on hand to save users time figuring out how much to reorder. These two criteria are the groundwork of automatic replenishment that generates restocking suggestions tailored to your business’s current replenishment needs.
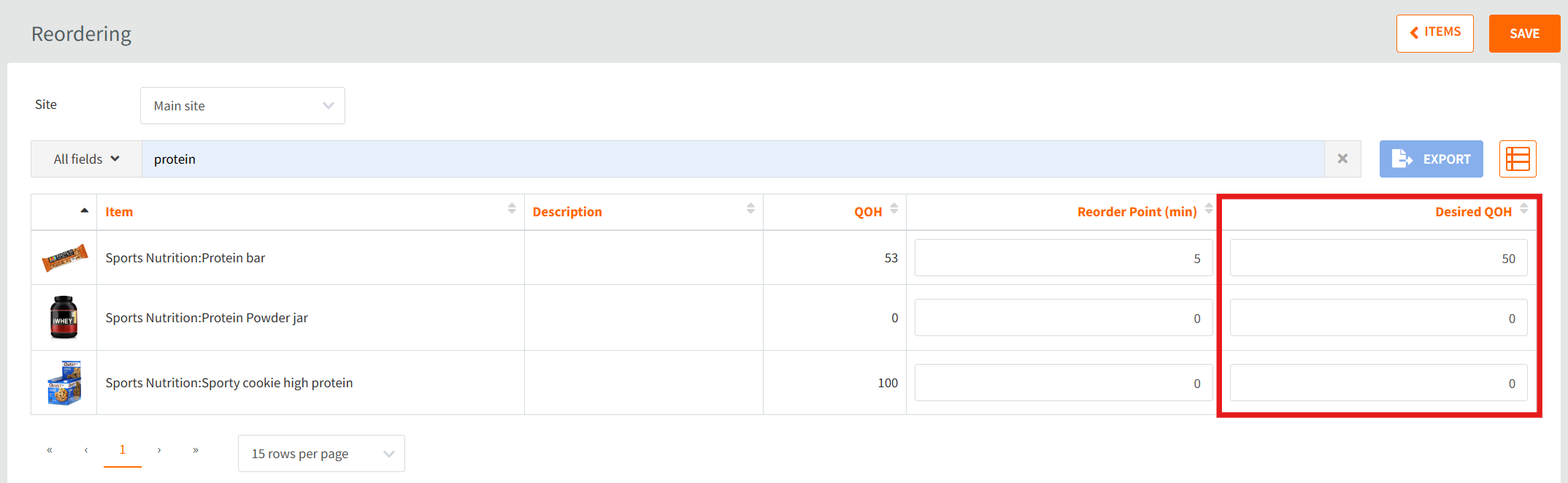
5. Cycle counting
Cycle counting is a method of regularly auditing a subset of inventory items on a frequent and ongoing basis. It’s up to you to determine the frequency and what item categories need auditing.
With automated inventory management apps, cycle counts cause minimal to no disruptions in operations. This is achieved through having your inventory barcoded, which makes scanning items into your system swift and efficient.
Cycle counts are often done from mobile devices for speed and convenience. Make sure your inventory software offers this mobile functionality.
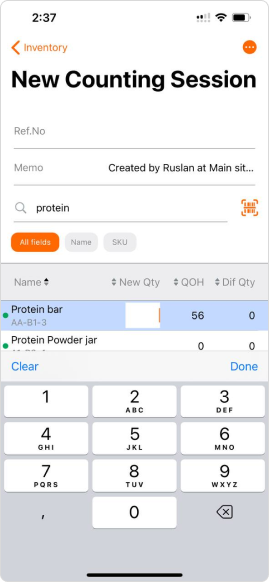
6. Physical inventory
Physical inventory is the process of physically counting and verifying the actual quantity of all the goods or products in a company's inventory. This involves counting all items on hand as opposed to cycle counts, where you set aside certain categories or individual SKUs for auditing.
In some inventory tracking solutions it goes by a complete or full inventory count. Once initiated, the software must bring all the quantities back to zero to let you enter the new quantities that reflect what you really have on hand.
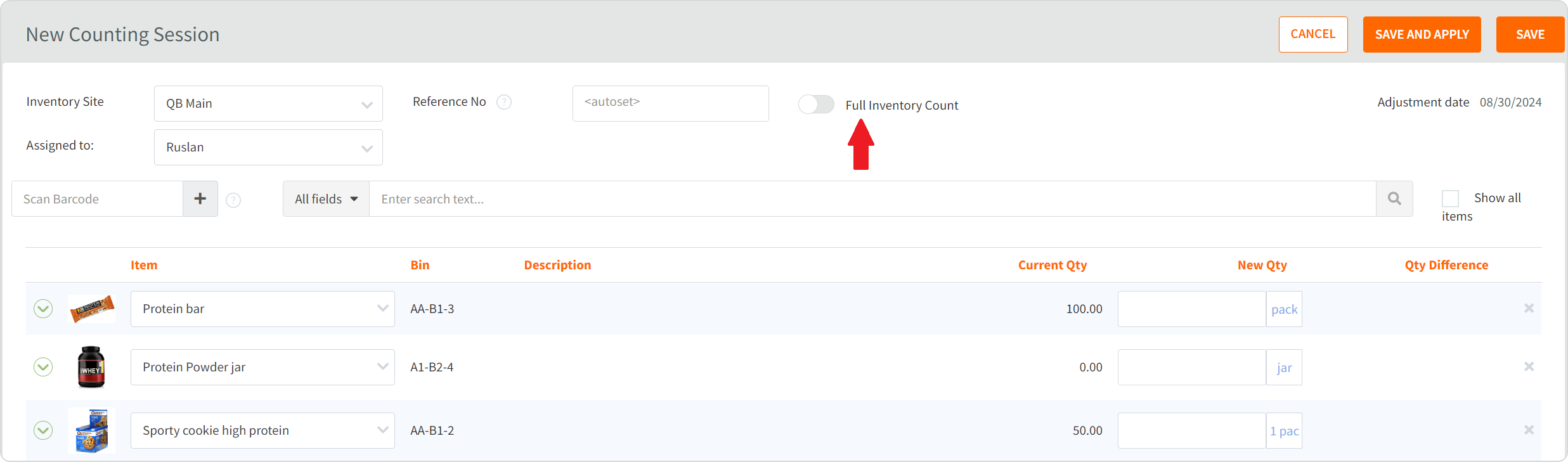
7. Batch tracking
Batch or lot number tracking is a practice of tracking groups of items with similar properties, like date of production, expiry, etc., to ensure a smoother recall process.
You must let your software know how these items should be treated (as serial- or lot-tracked) and then choose the tracking method. Some of the tracking methods include expiration dates.
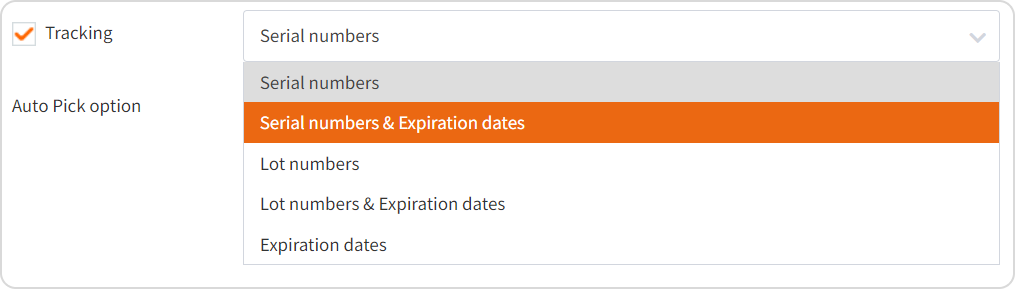
8. FIFO (First In-First Out) and FEFO (First Expired-First Out)
FIFO is a valuation method where goods produced or acquired first are disposed of before all the others.
FEFO makes sure products that expire sooner get sold first.
Inventory apps encourage you to pick either the FIFO or FEFO method for lot-tracked items. This way, your software will know which lots should go first on sales transactions, helping you keep your shelves stocked with newer items.
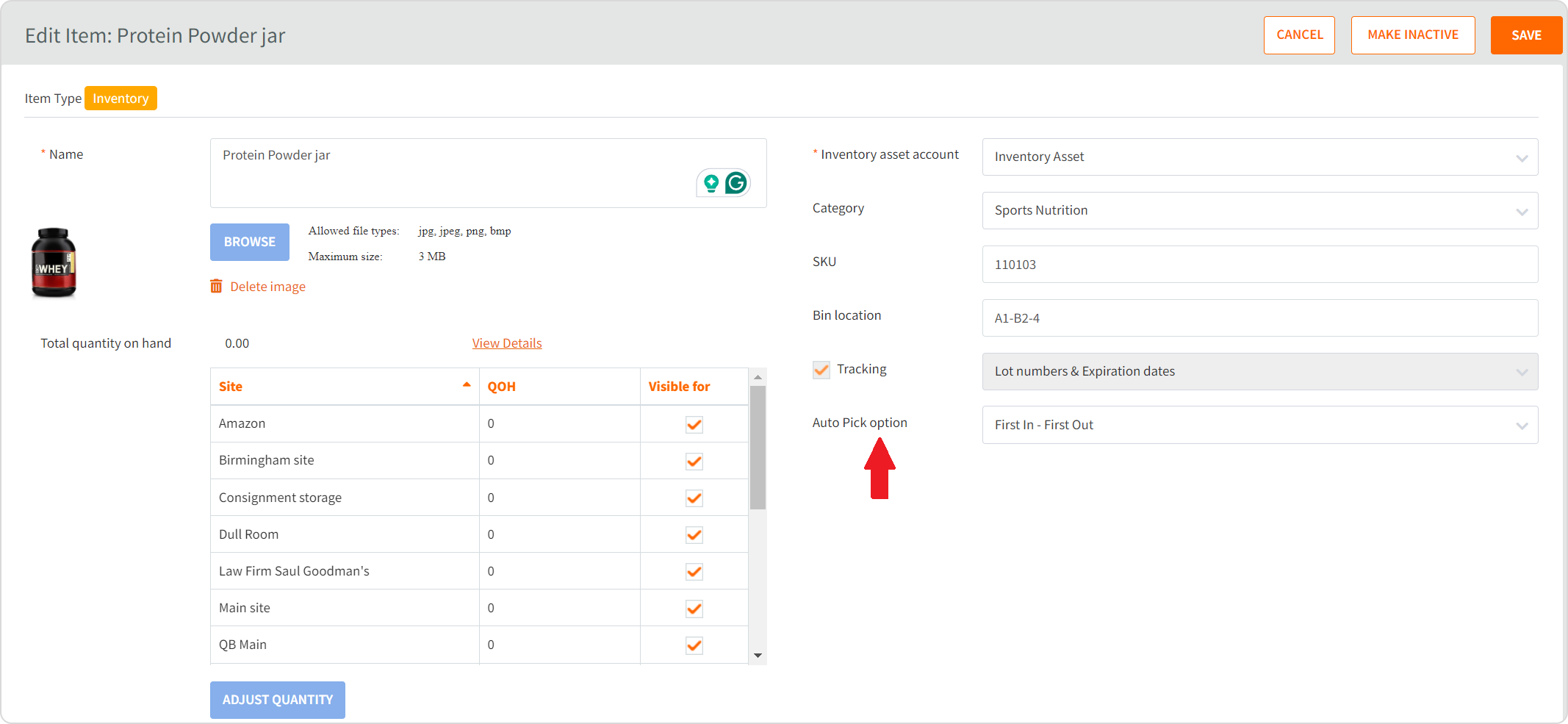
9. Bin location
A bin location is a specific storage spot within a warehouse or stockroom where an item is kept. It helps organize inventory efficiently, making it easier to find, pick, and restock items. Bin locations are usually labeled with a system of aisles, rows, shelves, and bins (e.g., A2-B5-S3 might refer to Aisle 2, Bin 5, Shelf 3).
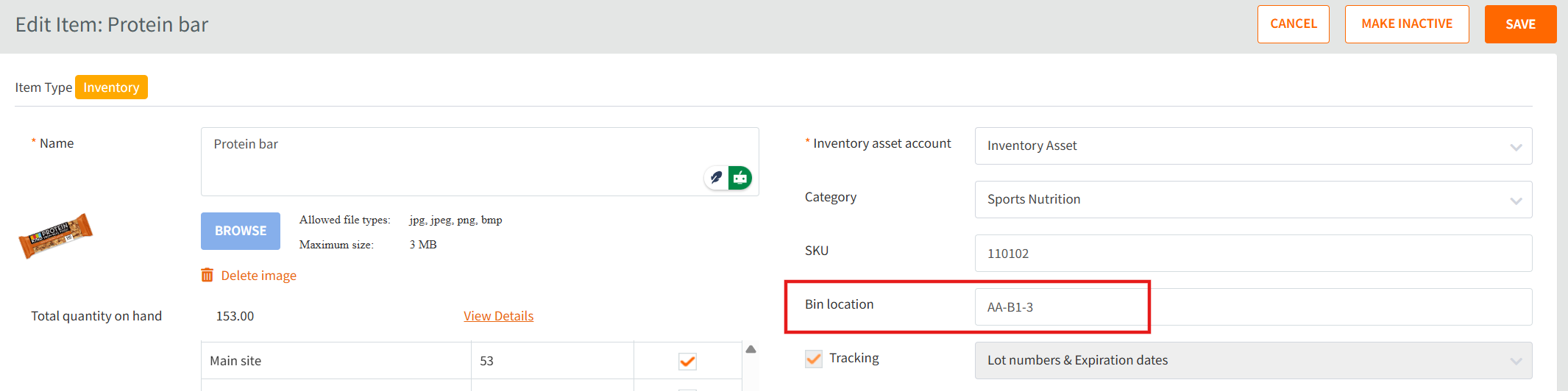
10. Bill of Materials
A BOM is a list of raw materials, components, sub-assemblies, and quantities needed to manufacture or assemble a product.
In stock control systems, they usually go by the same name, but you can also come across alternative terms such as manufacturing presets. BOMs help users navigate faster through the production or assembly process.

11. Price Levels
Price levels or price rules are a pricing strategy that helps businesses categorize and assign different prices to products or services based on certain criteria. This feature allows you to manage your pricing structures and tailor them to different customer segments.
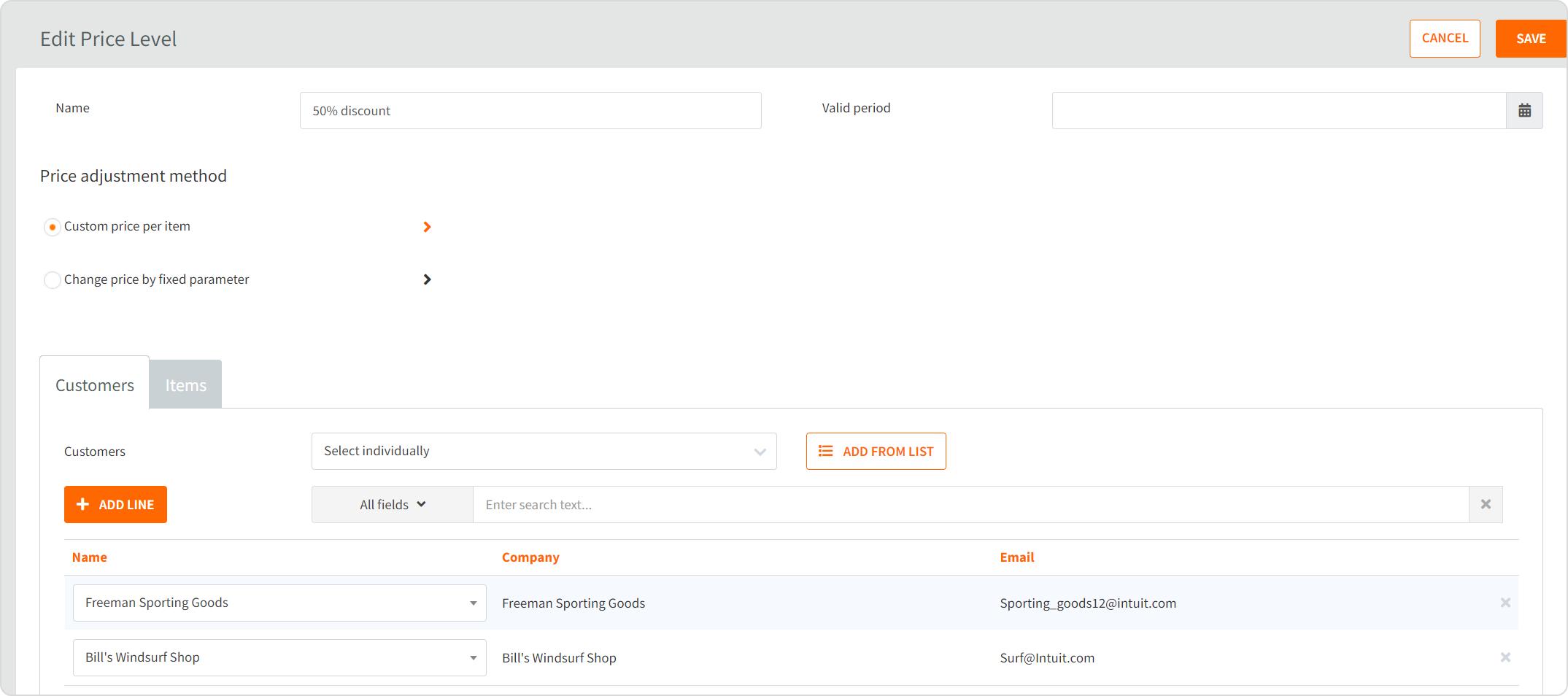
12. Negative Inventory
Negative inventory occurs when a system shows that there are fewer than zero units of a product in stock.
You can read more about why it happens and how to investigate and prevent the negative stock problem in our blog post here. One way to fight it is by disallowing inventory to fall below zero and getting warnings when it’s about to from your system.
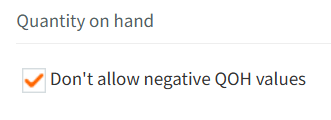
13. Unit of Measure (UoM)
Units of Measure (UoM) define how a product is counted, stored, bought, or sold. They ensure consistency in tracking stock and transactions.
UoM conversion is one of the most time-draining tasks if done manually. Inventory systems automate it, so you see only those UoM that are right for the current context of your work with inventory.
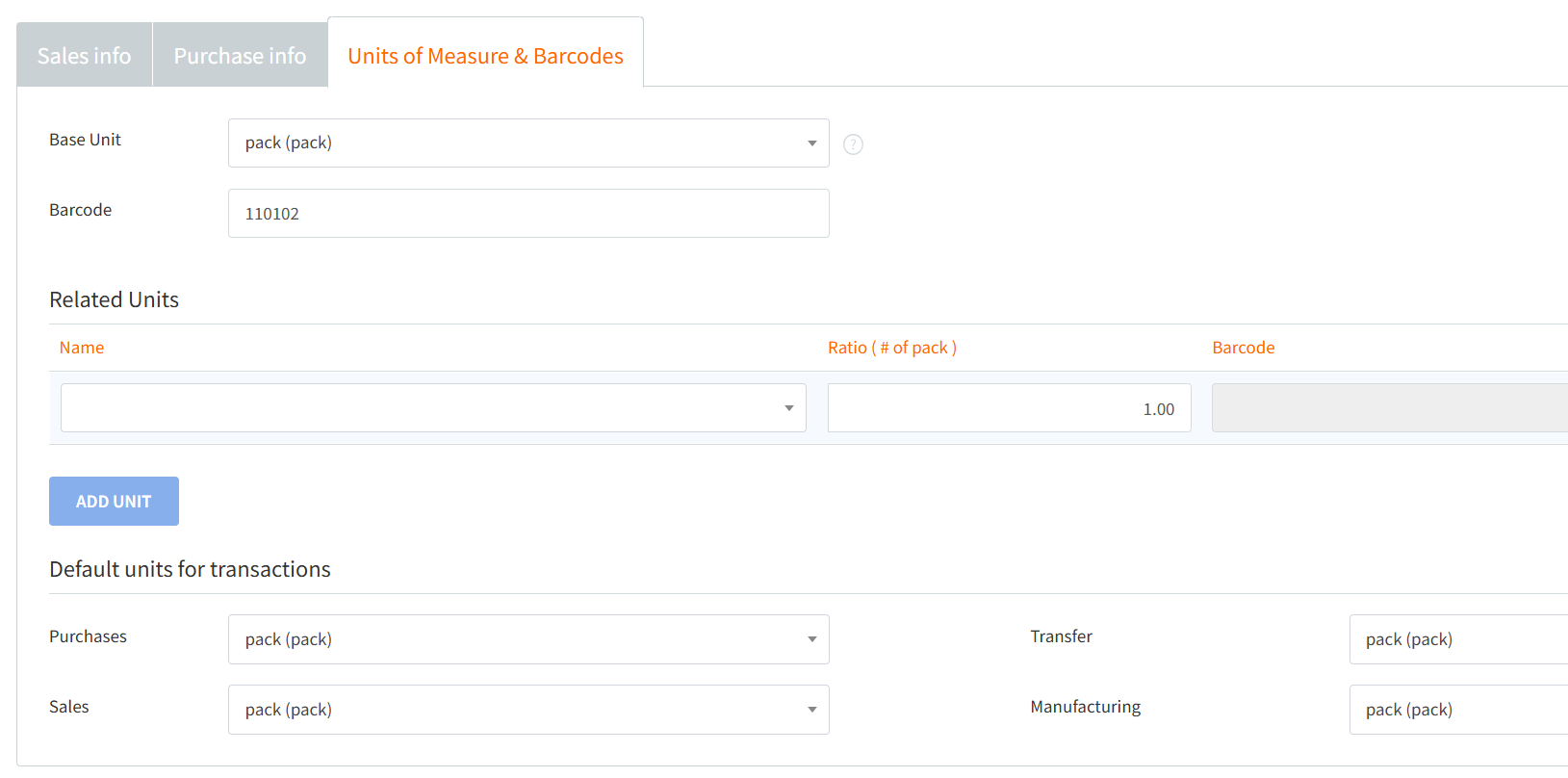
14. Barcoding
Barcoding in inventory management is a technology that uses machine-readable codes (barcodes) to track, manage, and identify inventory items quickly and accurately. It replaces manual data entry, reducing errors and improving efficiency. This functionality encompasses barcode generation, scanning, processing, and printing.
Today’s inventory control is unimaginable without barcodes. Just a heads-up - the assortment of barcode scanners can make the task of choosing one seem pretty daunting. We’ve curated a list of the best barcode scanners for small business needs here - check it out to make the right purchasing decision.
15. Preferred and Alternative Vendors
A preferred vendor is a supplier that a company prioritizes for purchasing goods or services due to factors like reliability, pricing, quality, and favorable terms.
Alternative vendors are backup suppliers that a company can turn to if the preferred vendor is unavailable, out of stock, unable to meet demand, or their pricing is simply too high at the moment.
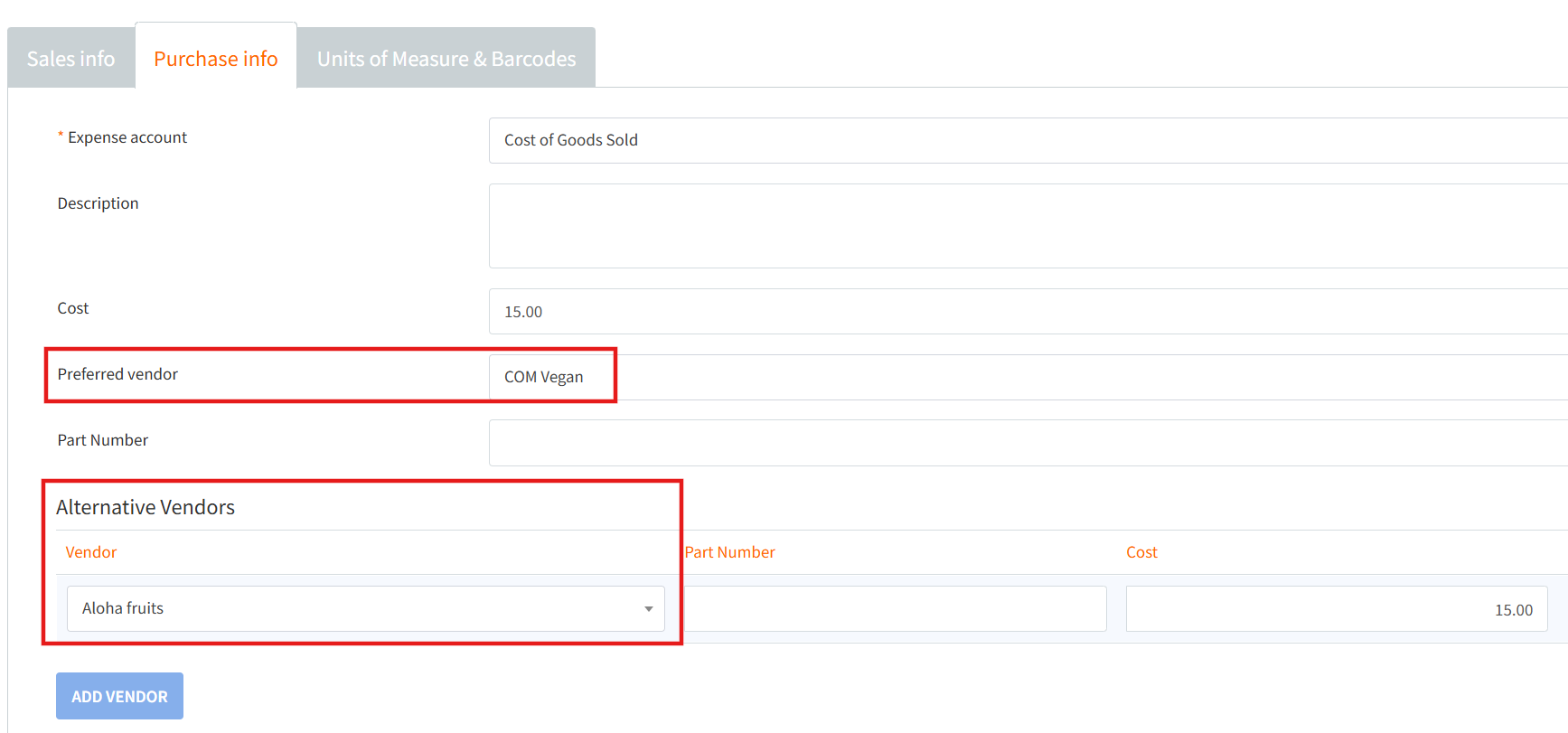
One inventory app to use them all - HandiFox Online
Today’s inventory control systems are the quintessence of advanced stock management practices, and HandiFox Online is no exception. Other than having all the inventory management terminology down, it can navigate you through the best ways to approach your inventory, purchasing, and sales tasks.
If you’re through with this inventory glossary, take the next step and see how it all works in HandiFox Online.